Выбор обработки поверхности - это проблема, с которой сталкивается каждый дизайнер. Существует много типов вариантов обработки поверхности, и дизайнер высокого уровня должен не только учитывать экономику и практичность дизайна, но и обратить внимание на процесс сборки и даже экологические требования. Ниже приведено краткое введение в некоторые обычно используемые покрытия для крепежных элементов на основе вышеуказанных принципов, для справки со стороны практикующих крепеж.
1. Электрогалванизация
Цинк является наиболее часто используемым покрытием для коммерческих крепеж. Цена относительно дешевая, а внешний вид хорош. Общие цвета включают черный и военный зеленый. Тем не менее, его антикоррозионные характеристики являются средними, а его антикоррозионные характеристики являются самыми низкими среди слоев цинкового покрытия (покрытие). Как правило, тест на нейтральную соль на распылении оцинкованной стали проводится в течение 72 часов, а специальные герметизирующие агенты также используются для обеспечения того, чтобы тест нейтрального соль длится более 200 часов. Тем не менее, цена стоит дорого, что в 5-8 раз больше, чем у обычной оцинкованной стали.
Процесс электрогалванизации подвержен водородным охлаждению, поэтому болты выше 10.9, как правило, не обрабатываются гальванизацией. Хотя водород может быть удален с помощью печи после покрытия, пассивирующая пленка будет повреждена при температуре выше 60 ℃, поэтому удаление водорода должно быть выполнено после гальванизации и до пассивации. Это имеет плохую работу и высокие затраты на обработку. В действительности, общие производственные заводы не активно удаляют водород, если не предписывается конкретным клиентам.
Последовательность между крутящим моментом и силой затягивания оцинкованных крепеж является плохая и нестабильная, и они, как правило, не используются для соединения важных деталей. Чтобы улучшить согласованность предварительной нагрузки крутящего момента, метод смазочных веществ покрытия после покрытия также может использоваться для улучшения и улучшения согласованности предварительной нагрузки крутящего момента.
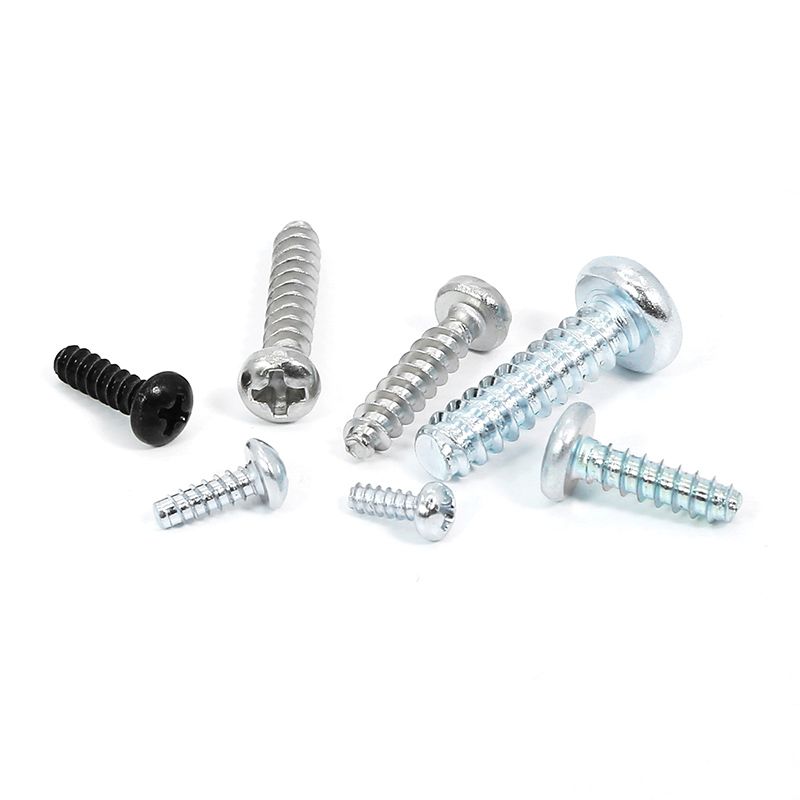
2. Фосфалирование
Основной принцип заключается в том, что фосфалирование относительно дешевле, чем гальванизирующее, но его коррозионная стойкость хуже, чем гальванизирующая. После фосфалирования нефть должно применяться, и его коррозионная стойкость тесно связана с производительностью применения масла. Например, после фосфалирования, применение общего масла против ржавчины и проведение нейтрального теста на соль всего 10-20 часов. Применение высококлассного масла против ржавчины может занять до 72-96 часов. Но его цена в 2-3 раза больше, чем у общего фосфалирующего масла.
Существует два широко используемых типа фосфалирования для крепежных изделий: фосфалирование на основе цинка и фосфалирование на основе марганца. Фосфалирование на основе цинка обладает лучшими характеристиками смазки, чем фосфалирование на основе марганца, а фосфалирование на основе марганца обладает лучшей коррозионной устойчивостью и устойчивостью к износу, чем цинк. Его можно использовать при температуре от 225 до 400 градусов по Фаренгейту (107-204 ℃). Особенно для связи некоторых важных компонентов. Например, соединительные болты и гайки двигателя, головка цилиндра, главное подшипник, болты маховика, колесные болты и гайки и т. Д.
Высокие прочности используют фосфалирование, что также может избежать проблем с охлаждением водорода. Следовательно, болты выше 10,9 в промышленном поле обычно используют обработку поверхности фосфалирования.
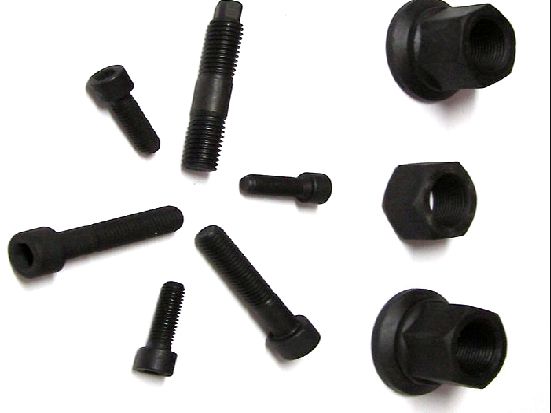
3. Окисление (почернение)
Чернило+смазок - это популярное покрытие для промышленных крепеж, потому что оно самое дешевое и хорошо выглядит перед расходом топлива. Благодаря его почернению, он почти не обладает способностью профилактики ржавчины, поэтому он будет быстро ржаветь без масла. Даже при наличии масла тест на солевые распылитель может длиться всего 3-5 часов.
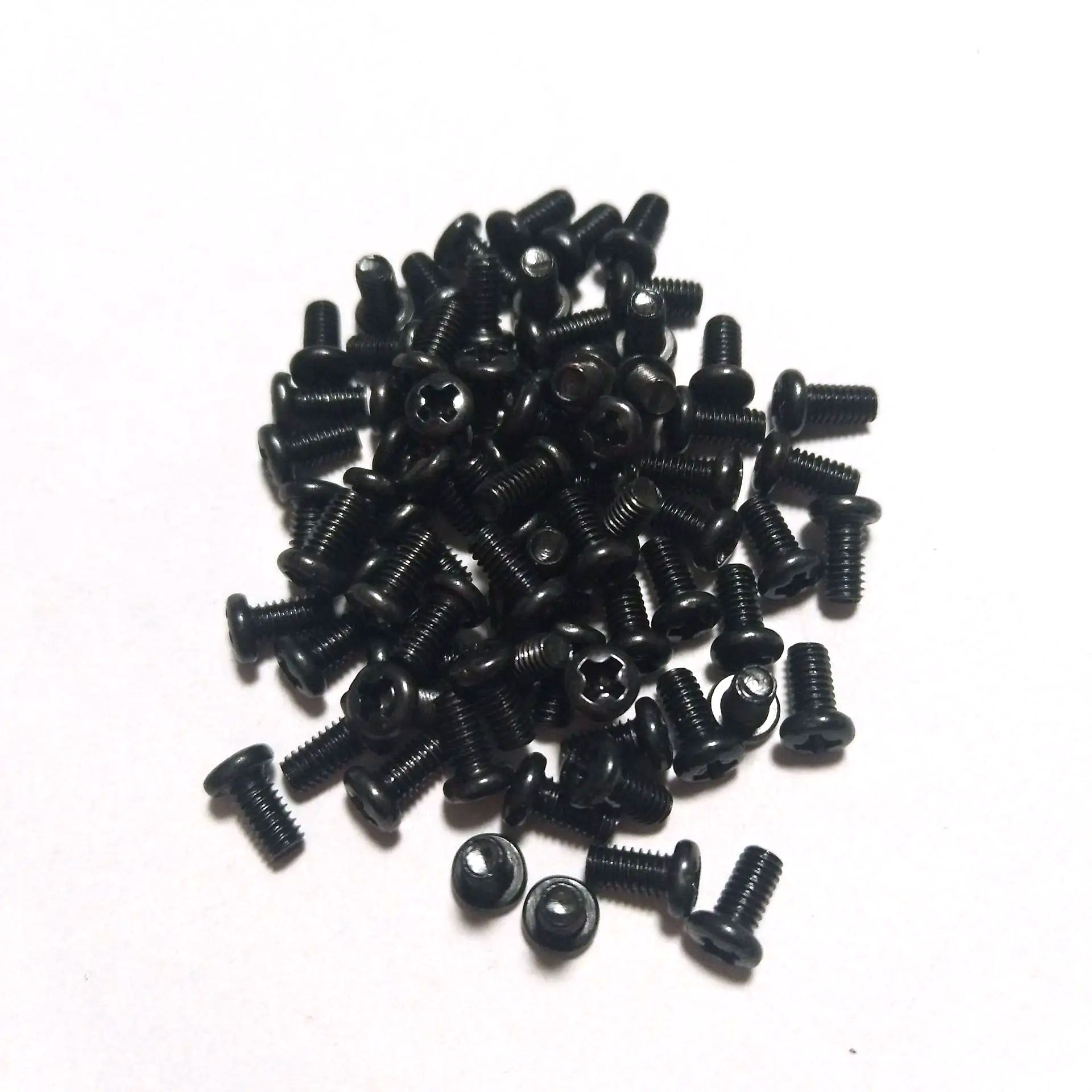
4. Объем раздела
Кадмиевое покрытие обладает превосходной коррозионной устойчивостью, особенно в морской атмосферной среде, по сравнению с другими поверхностными обработками. Стоимость очистки жидкости отходов в процессе гальванизации кадмия высока, и его цена примерно в 15-20 раз больше, чем у гальванизации цинка. Таким образом, он не используется в общих отраслях, только для конкретных сред. Застежки, используемые для нефтяных буровых платформ и самолетов HNA.
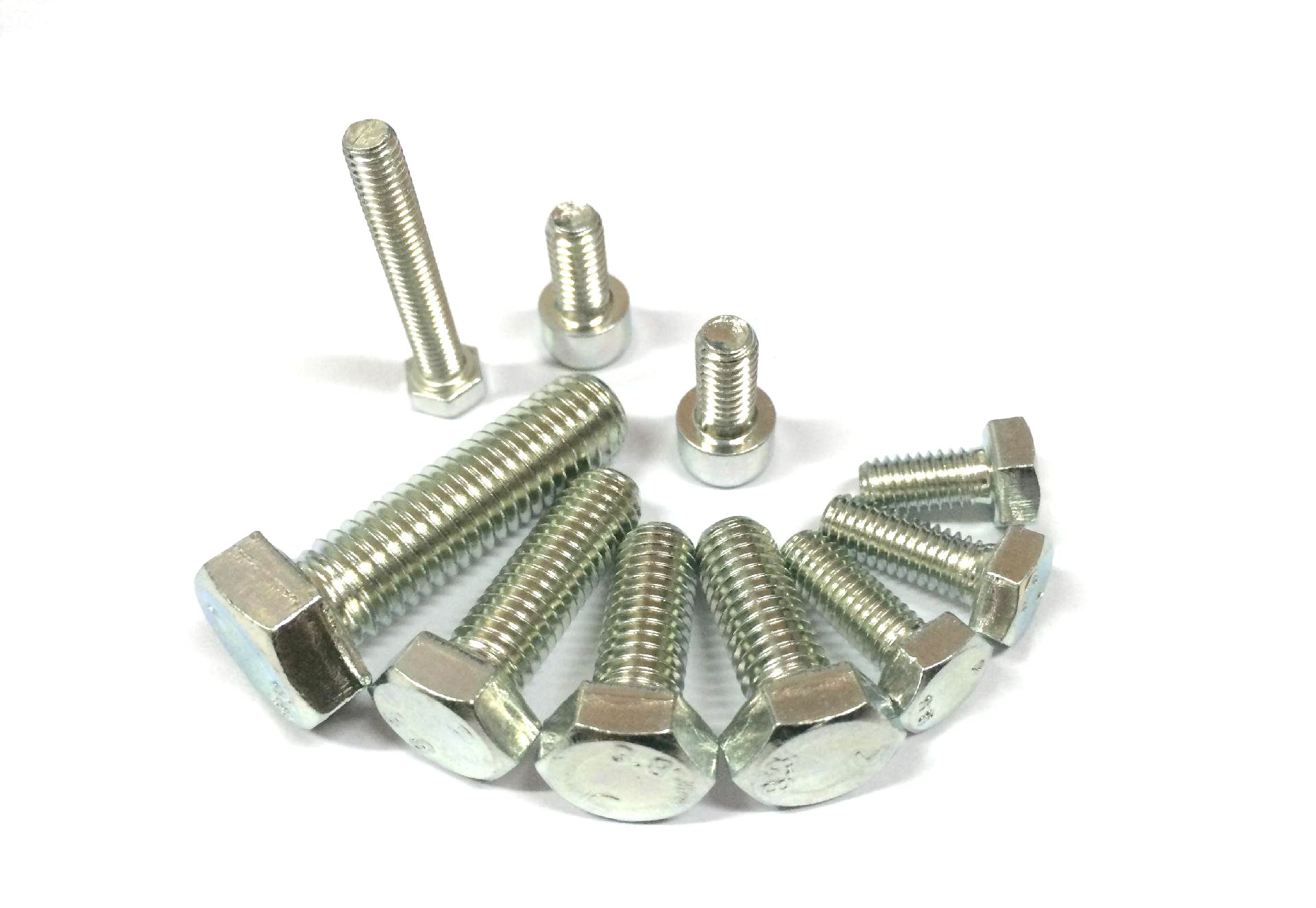
5. Хромовое покрытие
Хромовое покрытие очень стабильно в атмосфере, нелегко изменить цвет и потерять блеск, а также имеет высокую твердость и хорошую стойкость к износу. Использование хромового покрытия на крепежах обычно используется для декоративных целей. Он редко используется в промышленных областях с высокими требованиями к коррозии, так как хорошие хромированные крепежные элементы одинаково дороги, как нержавеющая сталь. Только когда прочность из нержавеющей стали недостаточна, вместо этого используются хромированные крепежные элементы.
Чтобы предотвратить коррозию, медь и никель должны быть высечены первыми перед хромированным покрытием. Хромовое покрытие может выдерживать высокие температуры 1200 градусов по Фаренгейту (650 ℃). Но есть также проблема охрушения водорода, аналогичная электрогалванизации.
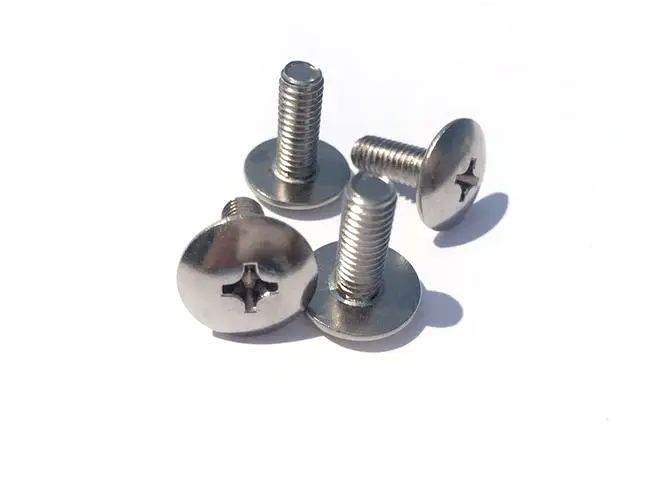
6. Никелевое покрытие
В основном используется в областях, которые требуют как антикоррозии, так и хорошей проводимости. Например, исходящие терминалы транспортных батарей.
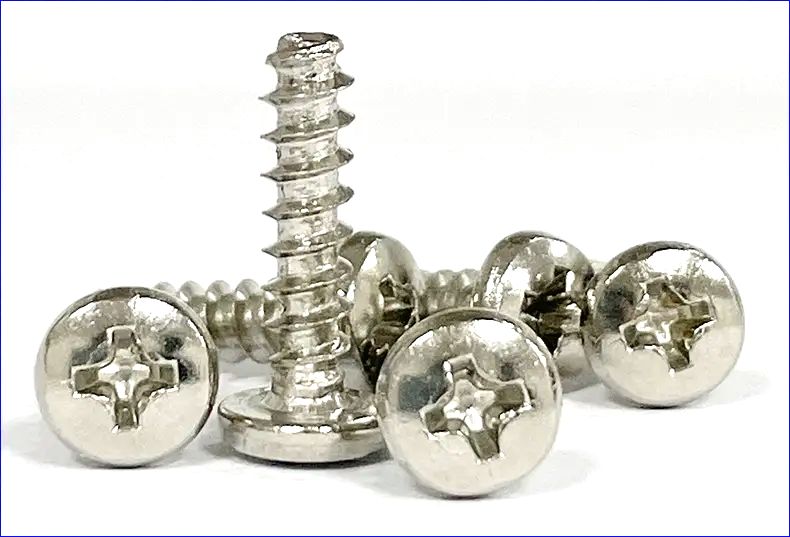
7. Горячая оцеливание
Горячая погружение - это тепловое диффузионное покрытие цинка, нагретое до жидкости. Толщина покрытия составляет от 15 до 100 мкм. И его нелегко контролировать, но обладает хорошей коррозионной стойкостью и часто используется в инженерии. Во время процесса оцинкования горячих пауток существует серьезное загрязнение, включая цинк отходов и цинк.
Из -за толстого покрытия оно вызвало трудности в привинтке во внутренних и внешних резьбах в крепежах. Из-за температуры обработки гальванизации горячей дип, ее нельзя использовать для крепеж, выше 10,9 (340 ~ 500 ℃).
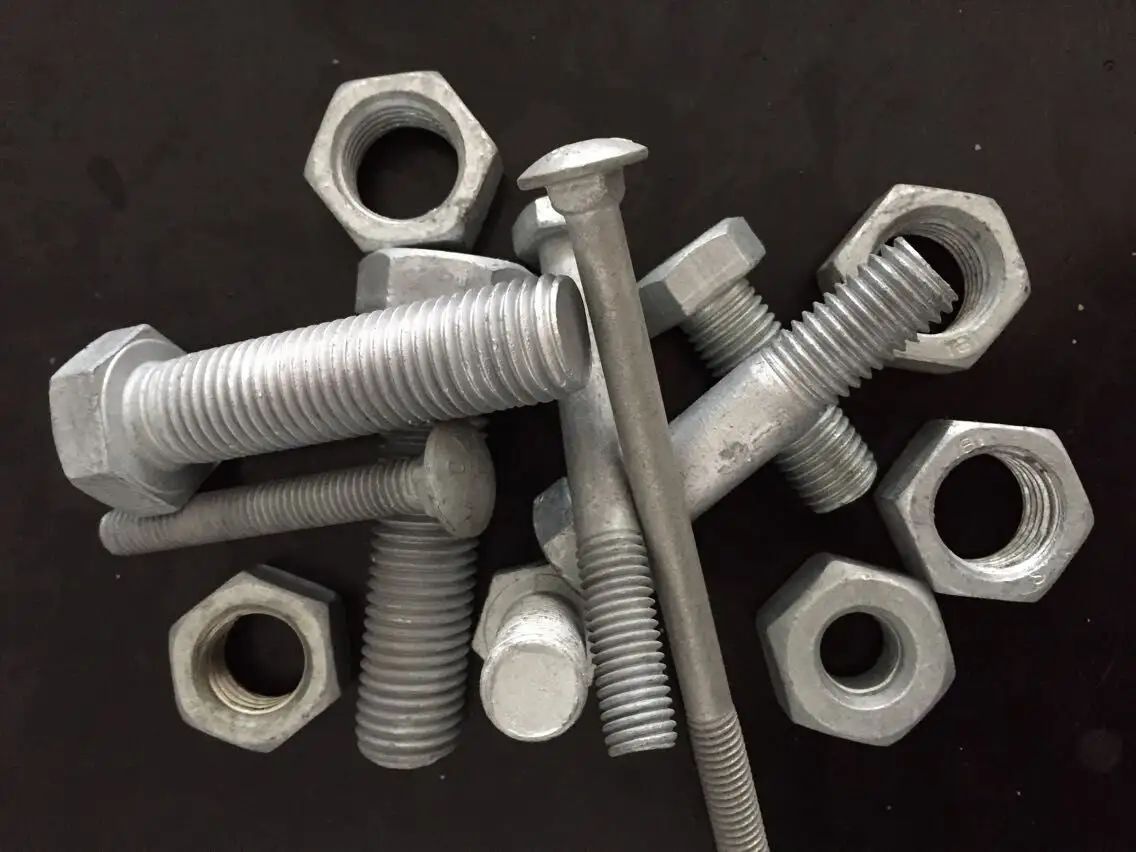
8. Инфильтрация цинка
Инфильтрация цинка представляет собой твердое металлургическое термическое диффузионное покрытие порошка цинка. Его однородность хороша, а в плане и слепых отверстиях можно получить равномерный слой. Толщина покрытия составляет 10-110 мкм. И ошибка можно контролировать на уровне 10%. Его прочность на связывание и производительность антикоррозии с подложкой являются лучшими в цинковых покрытиях (такие как электрогалванизация, гальванизация горячих уколов и дакор). Его процесс обработки без загрязнения и самый экологичный.
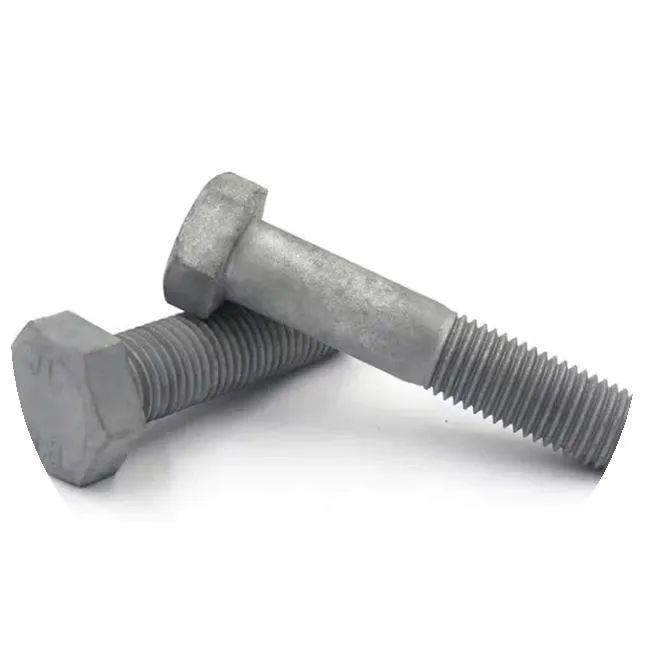
9. Дакромет
Там нет проблем с охлаждением водорода, и производительность последовательности предварительной нагрузки крутящего момента очень хороша. Не рассматривая проблемы хрома и окружающей среды, DacRomet на самом деле является наиболее подходящей для высокопрочных крепеж с высокими требованиями против коррозии.
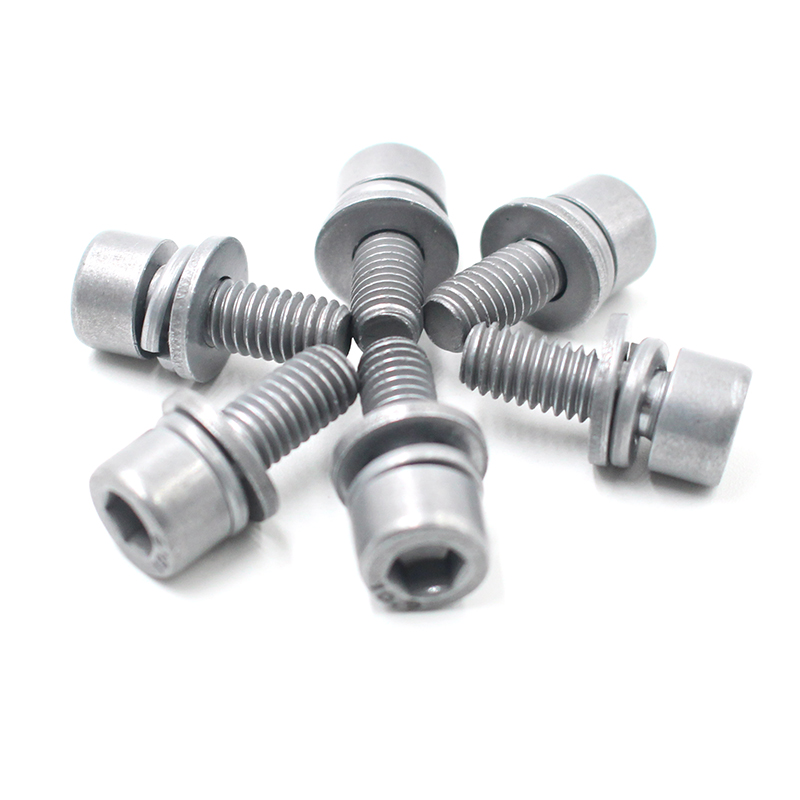
Время публикации: май-19-2023